Introduction
The performance and reliability of Gallium Nitride (GaN) power amplifier (PA) devices are highly dependent on their operating temperature. This article reviews the fundamentals of thermal resistance metrics, specifically focusing on the methods used for measurement and modeling to determine thermal resistance. Additionally, it explains the underlying principles behind these figures. Furthermore, the article highlights the relationship between thermal resistance, the maximum channel temperature listed in data sheets, and its implications for reliability predictions.
Ampleon’s methodology for GaN thermal characteristics represented in datasheets follows the process illustrated in Figure 1. The surface temperature (Ts) of the active die is measured using an Infrared (IR) camera and the case temperature (Tc) with a thermocouple, to extract the thermal resistance of surface to case (Rth(s-c)). The calibrated finite element analysis (FEA)-based thermal model is used to predict the channel temperature (Tch) for thermal resistance of channel to case (Rth(ch-c)). In addition, the lifetime tool can predict the Median-Time-To-Failure (MTF is the time that 50 % of the population has failed) vs power and channel temperature in a device. For specific calculation, we refer to the Lifetime Calculator on the Ampleon’s website. Pulse thermal impedance and temperature dependency of thermal resistance can be presented in the datasheet for specific devices.
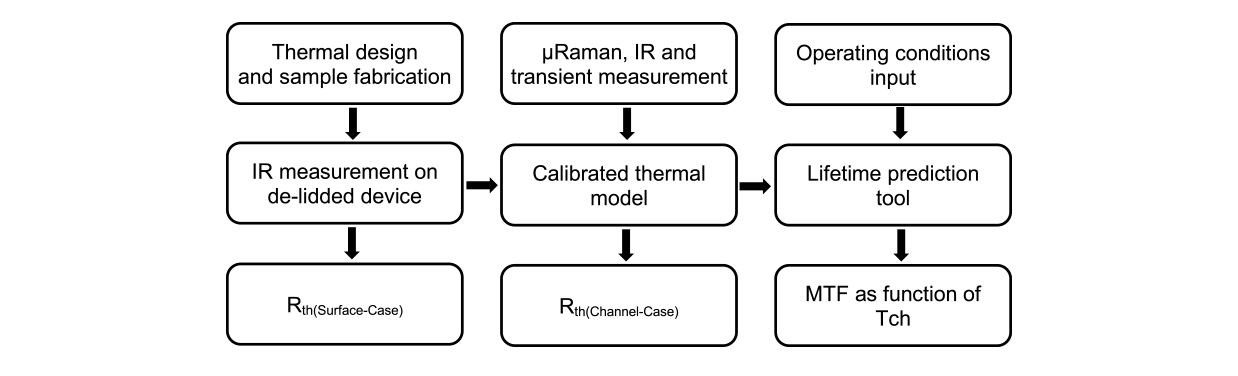
Figure 1. GaN thermal characterization process
The commonly used technique to measure the temperature of a power amplifier device under operation is using IR thermography. However, we should consider the limitations of averaging the temperature over optical spot size on surface and sample preparation. Ampleon’s datasheets present Rth(s-c) based on IR measurements to enable application of customers’ system-level IR measurement data, and comparison with the other thermal data.
The schematic of the IR measurement setup is illustrated in Figure 2. For visibility of die, packaging layer of ceramic lead is removed or overmold compound is etched away. The exposed die is coated with a high emissivity coating to obtain an accurate fixed emissivity value. The surface temperature (Ts) of sample is measured by the high-resolution IR camera from top view and the case temperature (Tc) of the package is measured by a spring-loaded thermocouple. The thermal resistance between surface to case is calculated as:
where the dissipated power (PD) is calculated as:
where Pin and Pout are the RF input and output power, and PDC is the DC input power.
Due to the nonlinearity of material properties, the thermal resistance slightly depends on heat dissipation and case temperature. Please refer to the specific product data sheet for the conditions under which the devices are measured.
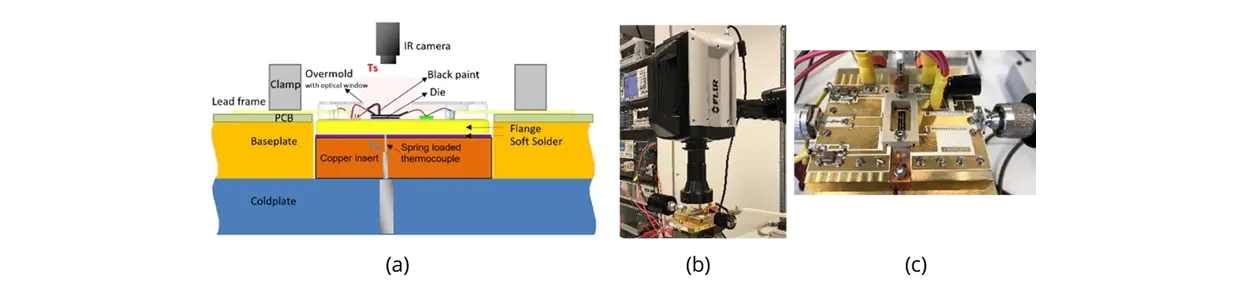
Figure 2. (a) Schematic, (b) image of setup and (c) board of the IR measurement
Accurate determination of the channel temperature relies on finite element thermal modeling calibrated with measurement. Ampleon’s datasheets present Rth(ch-c) based on thermal modeling to enable lifetime prediction and ensure to keep the device within thermal safe operation area.
For each process technology, the thermal model is calibrated on material properties and geometry with accurate IR and µRaman measurements on various steady heat dissipations, beside to transient electrical-based measurement. The calibrated model is benchmarked to make sure about the versatility and range of applicability. Figure 3 shows the measured IR image and modelled temperature of device surface with 3 dies.
The model geometry is used to reproduce the IR measurement by averaging the simulated temperatures inside the IR focus spot. The highest channel temperature (Tch) of the device which is the maximum temperature of the model is used to calculate the thermal resistance between channel to case as following:
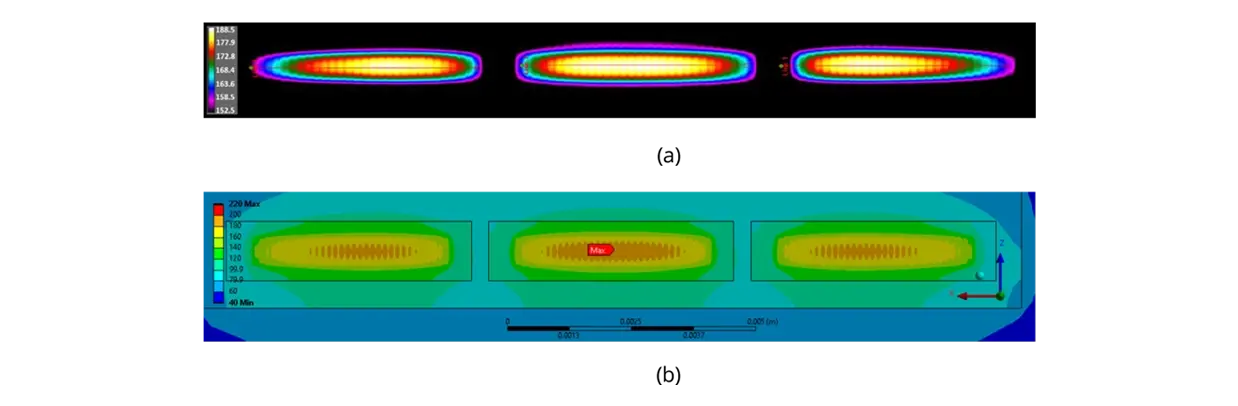
Figure 3. (a) IR-measured and (b) FEM-modelled of device temperature
About the author
Amir is a thermal modeling and characterization expert at Ampleon. He provides technical support to ensure products maintain optimal thermal performance and reliability over their lifetime.
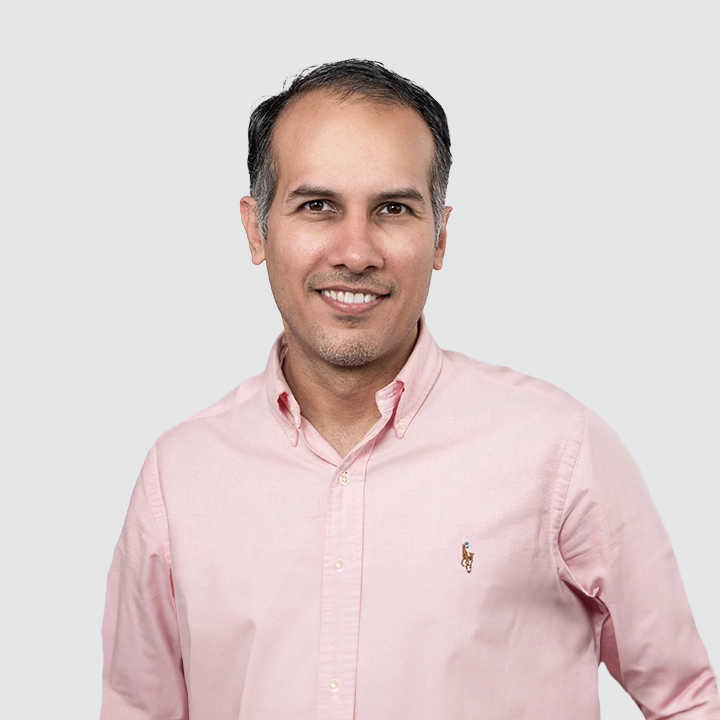
Principal Thermal Engineer
Committed to your success
During the entire process from design to delivery, we provide a range of support options to address your needs. Whether you require load-pull data, application boards, samples, ADS / AWR models, assistance with a complex design challenge or seek quick advice, we are on stand-by to support you. Our application engineering resources are spread around the globe, with our offices in Nijmegen / The Netherlands, Toulouse / France, Smithfield / USA, and Shanghai / China.
This tool provides reliable lifespan data, shown as Median-Time-To-Failure (MTF) based on Junction Temperature (TJ), assuming electromigration as the primary wear-out mechanism.
This tool provides real-time and precise data calculations for Junction Temperature, Thermal Resistance, Minimum Efficiency, and Thermal Efficiency.
From precise unit conversions to thermal resistance calculations and device lifetime estimates, our tools provide accurate, customizable solutions for your design needs. Explore our product selectors and latest RF power simulation models to optimize your projects effectively.